Trending: The Rise of Prefab and Modular Commercial Construction Techniques
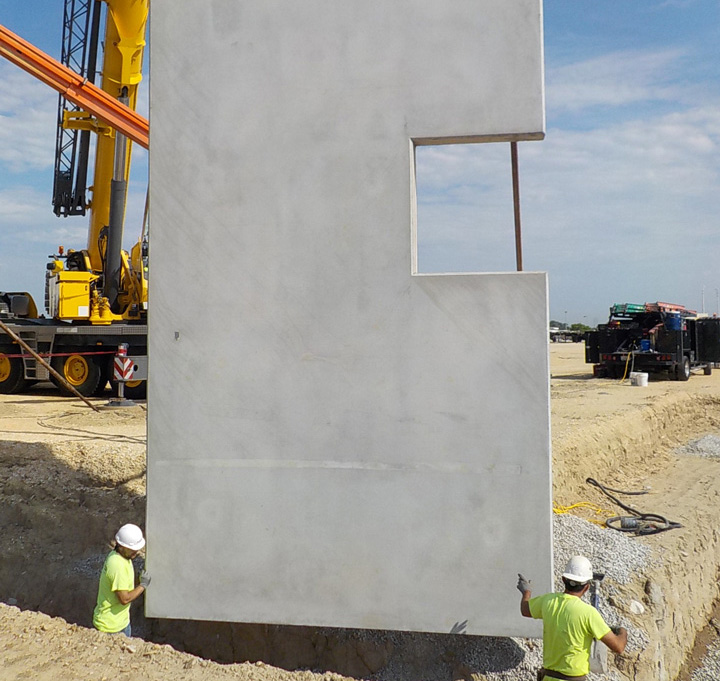
Something we’re hearing a lot about in our industry right now is the growing trend and popularity of prefab and modular commercial construction solutions. Much of this conversation is driven by the fact that in a business where actual building techniques haven’t changed much in decades, there’s a real hunger for new strategies to improve construction operations and control budgets – particularly in a commercial construction landscape where costs are rising and labor comes at a premium due to workforce shortages.
Using prefabricated construction components (elements that are manufactured off-site and then delivered to the construction site for installation) or a modular construction model (where entire building sections are constructed in a plant facility and delivered for on-site assembly) certainly has the potential to improve efficiencies. Not all that long ago, when I was still a young laborer in the field, many items such as millwork, ductwork and mechanical components were still frequently fabricated on the job site. Back then, many “old timers” predicted prefabrication was the future.
Sure enough, as the cost and time savings of manufacturing elements off-site were realized, prefabrication and modular models evolved over the years and became more commonplace, and the type and variety of elements being prefabricated expanded. Millwork is now being delivered fully assembled and even with under-cabinet lighting pre-installed, full electric panels are being built off-site, and modular building sections are nearly plug-and-play when they arrive on the job site. This shift has taken place just over the course of my 27-year career as a commercial general contractor, and I expect prefabrication and modularization will become increasingly important – and used in new and innovative ways.
Here are some reasons why:
- Component Costs: If a shop is set up to manufacture a specific item off-site, as opposed to creating it in a make-shift workshop on a job site, it typically saves time and therefore money. And when we step up from prefabricating items such as millwork and ductwork to larger, more complex elements – such as prefab electrical rooms that get installed in a space, or prefab refrigeration structures that are lifted to a facility’s roof – and modular components – such as full hotel suites – the efficiencies to be realized scale up too.
- Scheduling: Anything that can be pre-built and brought to the job site is always going to help the overall commercial construction schedule. Not only are these elements not subject to some of the typical construction job site delays – from weather-related holdups to critical path issues – but they also help the overall schedule thanks to the relative ease and speed of installation.
- Labor Costs: Labor in a shop or manufacturing facility is usually cheaper than labor on a job site. That can be due to several factors, from the skill level required (in a shop, employees are trained for a specific task, whereas on a construction job site, workers must have a broad skill set) to the job setting itself (a shop is a more controlled environment whereas a construction site has more inherent hazards and risk that must be managed).
- Labor Efficiencies: Plus, on-site labor needs are more streamlined for prefabricated items. Look at the installation of pre-cast concrete walls. Basically, all you need is a crane operator to lift the sections off the truck they were delivered on, and several workers to guide and set the sections in place. Compare that to building a traditional masonry wall, which requires delivering materials, setting up scaffolding, mixing mortar and building the wall one piece at a time.
While it’s easy to look at the pros, more widespread use of prefabrication and modularization also poses some new questions, challenges and considerations:
- Logistics: While utilizing prefab and modular models can improve efficiency on a construction job site, they do entail extra planning in terms of shipping and delivery logistics, as well as capacity for storing these element on the job site until they are needed.
- Municipality Inspections: In a traditional construction process, rough inspections at various stages allow the municipality’s inspectors multiple opportunities to see the inner details of systems and components while they are visible and ensure everything is up to code. As more, larger and increasingly complex components are prefabricated off-site – and in some cases at out-of-state facilities – how will this impact the inspection process for municipalities?
- Union Considerations: As prefabricated elements and modular components become more sophisticated and more commonplace, will the shops where they are manufactured be unionized? In union towns like Chicago, this has the potential to raise sensitivities if work traditionally done by unionized field laborers shifts over to non-union, off-site shops.
Regardless of the answers to these questions, there’s no doubt our industry will continue to evolve – and it’s exciting to see how changes in processes and techniques will impact our business for the better.
Tel: 847-233-9200 x712

Questions? Comments?
You can reach me at CTaylor@eci.build
www.EnglewoodConstruction.com